Text and images: Juha Pokki, published in Koneurakointi 8/2023
In Finland, deliveries of new landfill compactors do not take place every day, which is quite understandable: there have been a lot of changes to the number and operation of open landfills over the past ten years. In Kouvola, however, the local landfill operator boldly looked to the future by investing in a new TANA H450eco landfill compactor.
On the drive to the Keltakangas waste treatment centre in Kouvola, a song is playing on the radio in which the singer contemplates whether wild horses still exist. To be honest: I don’t know. But ask whether there are still any landfill compactors! I can say straight away that you can indeed find them, even though they too have become increasingly rare, especially compared to the situation in the 1990s. When it comes to manufacturing them, Finland has a long tradition in this field.
Tana has been manufacturing landfill compactors since the early 1970s, and even though deliveries in Finland can number fewer than one per year – a few per decade would be good these days – there is still demand here for new machinery. A suitable and at the same time rare example can be found in Keltakangas, where a new TANA H450eco was delivered to the landfill’s operator Kymenlaakson Jäte Oy in September 2023. Weighing a good 45 tonnes, the new landfill compactor will be used to compact waste well into the future.
Landfills have changed
The perception of landfills has undergone quite a change over the past 15 years. Firstly, on the whole, traditional open landfills have been modernised, not only in terms of their function, but also into so-called waste processing centres, where the incoming waste is sorted as much as possible for recycling. The most traditional form of waste, municipal waste, has practically disappeared, as disposing of organic waste in landfills has been prohibited since 2016. For example, here in Kouvola, the disposal of municipal waste in the landfill saw a sharp decline already years ago following the introduction of modern, certified waste incineration in Kotka, to which municipal waste flows have since been directed.
An open landfill can still be found here, but its material composition is very different compared to, say, the beginning of the 21st century. Household garbage bags can no longer be seen blowing around.
“Keltakangas is the only landfill in the Kymenlaakso region that complies with EU directives, and even though most of the waste can be delivered for reuse, depending on the year, around 5,000 to 10,000 tonnes end up in the landfill,” says Sanna Ahola, Processing Manager at Kymenlaakson Jäte Oy. “Last year, the number was about 7,700 tonnes, which corresponds to around five percent of all incoming waste,” Ahola continues.
Still lots to do in the future
In percentage terms, the amount may not sound very big, but measured in tonnes, it is still definitely a lot of work. So what does that number consist of? “Even though waste recycling is constantly developing, there will always be fractions that it is not possible or reasonable to use,” begins Samu Korjala, Maintenance Foreman.
“Only non-hazardous waste that is difficult or impossible to shred, is disposed of at the landfill. This waste includes certain types of industrial reject, such as fiberglass, wool, large pipes and so on,” he continues. Sanna Ahola adds to the list, for example, soil containing the seeds of invasive species, which of course cannot be used elsewhere due to the danger of the plants spreading. However, this type of waste is still suitable for the landfill.
Keltakangas has enough capacity for an estimated 30 years. The environmental permit was renewed in 2022, according to which there are half a million cubic metres of disposal space left. The maximum height for the waste fill is set at 83 metres. The new TANA H450eco was purchased to compact this pile.
Purchased for good reasons
Kymenlaakson Jäte Oy has had a TANA throughout the history of the landfill operator, since 1998, and the new machine is the fourth in the series. The previous machine was a smaller G260 model from 2004 that was purchased used. “The machine before that burned out, and it was replaced by a second-hand machine,” explains Samu Korjala. In autumn 2022, the team started planning a replacement for that TANA, which will soon be two decades old with 8,000 operating hours on the clock.
“Because we are a municipal operator, a tender had to be announced for the procurement, but only one offer was received: from Tana Oy,” says Korjala.
Bigger and more powerful
More weight was wanted, and more weight was delivered: the TANA H450eco is at the higher end of the new H Series that Tana launched in 2020 and weighs 45 tonnes. Compared to the previous G260, which weighed approximately 26 tonnes, the difference is significant, which can also be seen in its performance.
“This clearly does a better job,” says Janne Markkanen, who is operating the machine today. “It compacts better, and the machine is also wider than before. I don’t have to drive over the same places as many times,” he adds. In fact, the 3.8-meter track width is more than a meter wider than that of the smaller machine. The new model also has two full width drums with drive motors at each corner. “The work is lighter, and the machine feels good in every way. The electric steering is precise, and the cabin is quiet. It’s a nice place to work,” Markkanen confirms.
There is no lack of power either, as the Cummins 6-cylinder, 14.9-liter X15-C535 engine produces peak power of up to 580 horsepower when necessary. Torque is also impressive at 2644 Nm, while average fuel consumption is around 22 liters per hour.The crushing force is 229 kN, and the diameter of the drums is 1620 millimeters including the 200-millimeter crushing teeth, of which there are 110 on each drum. The ability to move forward and stability have been found to be excellent; as a rule of thumb, the operator tends to run out of courage sooner than the machine begins to lose gradeability.
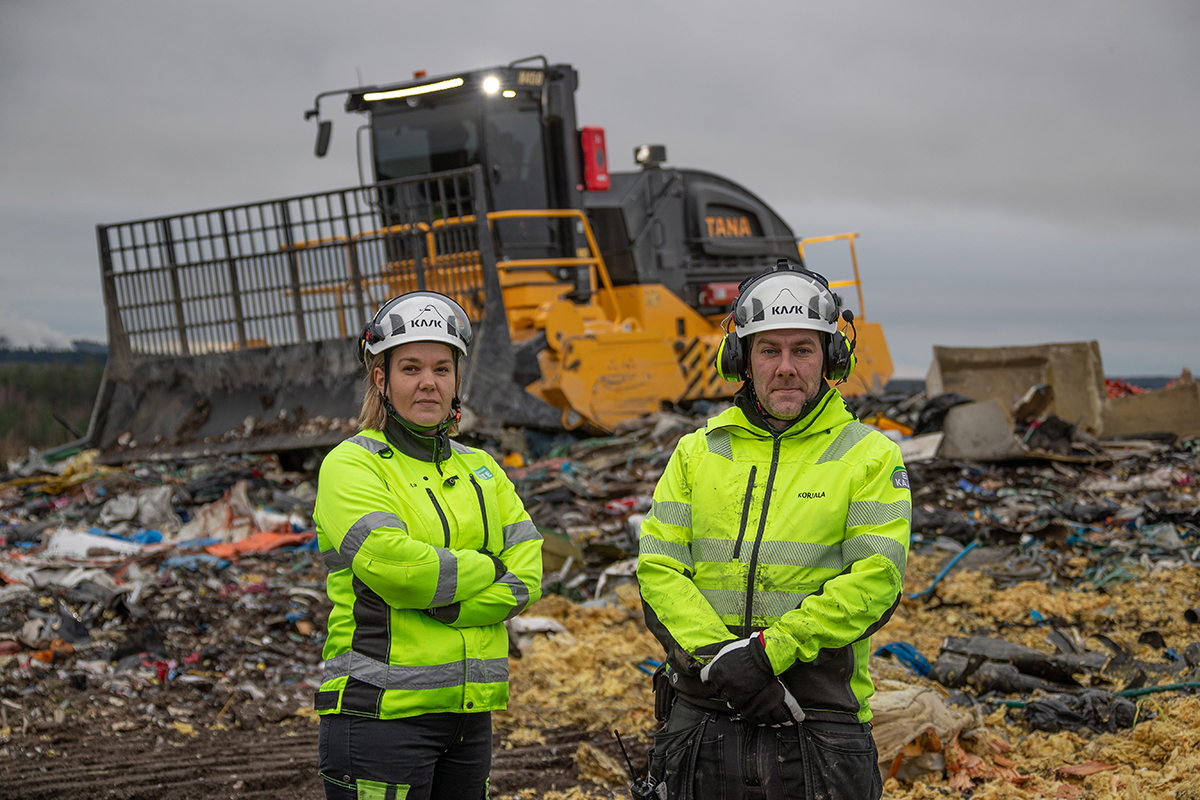
Investment in the future. Keltakangas still has enough landfill capacity for an estimated 30 years, and the new TANA will serve for much of this time, according to Sanna Ahola and Samu Korjala of Kymenlaakson Jäte Oy.
Good maintenance services and easy to control
The new machine has been warmly received at Keltakangas among the entire team. Even though there are two main operators, as many as 11 employees have been trained on the machine. “We intend to vary our work tasks, so it was natural to train more drivers on the new machine as well,” explains Sanna Ahola. “And now that we have this new machine, we also have enthusiastic operators,” adds Samu Korjala and continues: “Whereas with the previous machine it was a bit like having to tell someone to operate it, that is no longer the case. On the contrary, everyone wants a go!”
The new machine is not in continuous use but used only a few hours a day. The annual number of operating hours is estimated to be a moderate 300. Correspondingly, the machine is also expected to have a longer service life. “We expect to get 20 years out of it,” says Samu Korjala. This target is supported by the fact that with such a modern machine, maintenance and various problem situations are easier to predict.
“Before, we probably had more hard driving combined with poor maintenance,” Korjala laughs. “Now the machine has a maintenance contract, and there are also better opportunities for proactive maintenance,” he continues.
According to Sanna Ahola, the TanaConnect® remote monitoring system provides a good overview of the machine’s health. “I can access a lot of data that can be used to anticipate potential problems, and it also sends various notifications,” Ahola says, sitting at her computer. The importance of anticipating cannot be overemphasised in these kinds of conditions, and it has also been noted at Keltakangas.
The trailer compressor is a great accessory. For example, fiberglass dust is very good at clogging coolers and radiators if they are not cleaned, but this has also been taken into account in product development. At certain interval, the cooling fan blade angle changes and the air flow cleans the radiator, the housings have been improved, and so on,” says Korjala.
Rare and the best
When ordering the new machine, a few optional accessories were also specified by consulting with the operators. “When finalising our order, we went through all the equipment that could be justified to make the machine easy to work with and long-lasting,” says Sanna Ahola. Accordingly, tinted windows, auxiliary work lights and an auxiliary camera system were chosen for the cabin. The automatic fire suppression system is supplied by Dafo, and according to Korjala, this has been the practice for some time now on all new machines where it can be installed.
All in all, both Ahola and Korjala agree that the order was delivered without complications and even ahead of schedule. “The machine was supposed to arrive by the end of October, and it was delivered already in September,” says Ahola. The new machine has been in operation for well over a month now, and the rare purchase has lived up to expectations. “There’s no way around it: TANA really is the best landfill compactor in the world,” concludes Korjala. We certainly wouldn’t object, so let’s go with that!

The engine is easy to service thanks to the design of the engine cover, which opens wide. The dust protection was engineered to meet the challenges of waste treatment.