As waste management professionals, we are constantly facing the challenge of how to process problematic waste types. Tana Oy has a cost-efficient solution to offer for turning such waste streams into value. Shredding materials both minimises the space they consume and helps separate reusable materials, which in turn generate extra revenue.
Three most challenging materials to recycle
End-of-life tyres
Several machines needed to process them. With many machines the shredding process becomes inefficient and uneconomical. Furthermore, particle size requirements are often not met.
Mattresses
Impossible to compact and consume an immense amount of landfill airspace. This makes them expensive to dump, and metals are not recycled. In addition to this, there are not many shredders that can efficiently shred them.
Ragger wire
They are a by-product of producing recycled paper and should not end at landfill, but often do because they are a very tough waste to recycle. Ragger wire usually contains quite a lot of metal which turns into remarkable turnover when separated from the waste.
Tana Oy research and development has tackled the problem of all three waste types. There is a need and potential for processing these kind of materials, and they all require high torque and separation of metals. Also, particle size needs to be adjustable to meet the varying requirements of the usage of the shredded material. The TANA Shark slow-speed shredder meets all these requirements. It is capable of processing all the mentioned waste materials and many more for adequate particle size even in one pass. This both reduces the volume of waste and enables recovery of materials.
In addition to robust hardware design, the TANA Shark has an intelligent control system with preprogrammed operating modes. These preset operating modes optimise the shredding process based on waste type and expected level of contamination. Tyres, ragger wire and mattresses have their own programmed shredding modes. By using these programs, shredding is efficient and machine capacity is high. This keeps operating costs low and output levels high, and generates revenue.
Perfect separation and shredding of tyres in a single pass

Tyre shred and separated metal transform end-of-life tyres into revenue. One of the most popular uses is to separate the metals for recycling, and to use the tyre shred as fuel. Tyre shred from car and truck tyres is almost equal in heat value to gasoil and even 25% more effective than coal. The challenge here is the particle size and residue metal. Power plants have strict quality requirements for the tyre shred. The particle size has to be homogenous and no remnants of metal wires should be present.
To shred tyres cost-efficiently, the process has to be fast and operation costs in control. Using separate machines to shred, screen, and recover metals is not economical. Costs are high, and the process is slow. The TANA Shark shreds tyres and separates metals in one pass. With its in-built screen, it produces a very homogeneous 80mm particle size. What once was a problematic waste is now an efficient fuel or valuable reusable material.
Waste mattresses can generate revenue
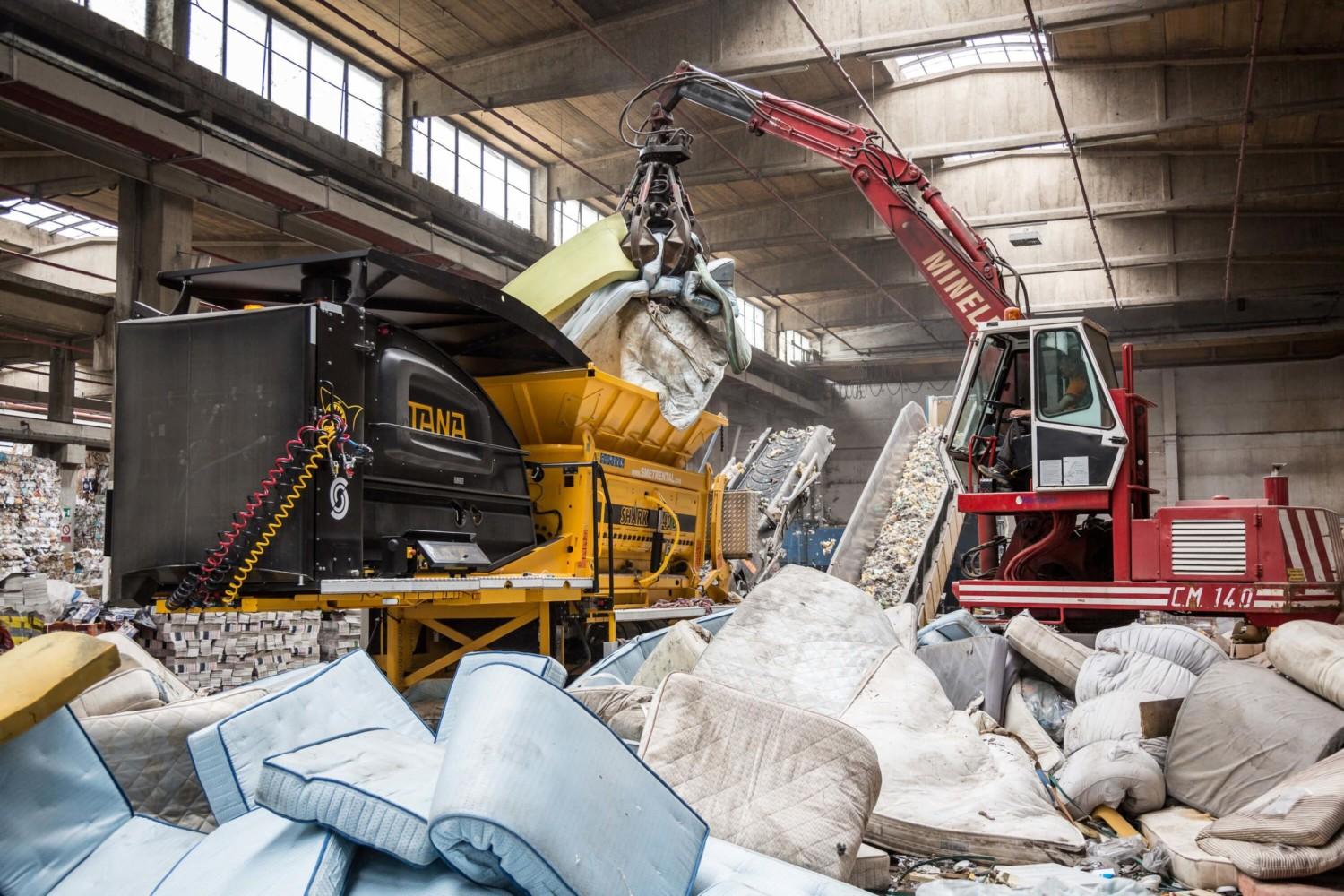
Instead of dumping mattresses at a landfill, they can be turned into valuable materials. The fluffy material may sometimes still end up in landfills, but the separated metal has value. Shredding mattresses opens up possibilities to generate more revenue. Separated steel springs is valuable scrap metal. Foam as fuel provides energy or after refining, foam provides carpet underlay or padding. Textiles and fibers are material for filters. Long textiles as well as the springs tend to wrap around the rotor and sometimes block it. With the TANA Shark this does not happen.
Even if you choose to landfill the mattresses, TANA Shark provides advantages. Shredded mattresses take up a lot less airspace and the shred is easy to compact at a landfill, which saves you money. Separating the metals during shredding is an easy source of extra income.
Turn the metal from ragger wire into profit

Total of 30-35 % of the wet ragger wire coming from the pulping process consists of steel wires. To get money out of the recycled metal, it has to be separated from the waste. TANA Shark’s over-band magnet pulls the metal out of the shredded mass. The Shark shreds approximately 8 tons of ragger wire per hour. At this speed, the TANA Shark produces 2.5 tons of recovered steel per hour. This steel can then be sold and recycled for extra income.
Rest of the material is plastic, and when dried, it is ready-to-burn RDF. It has a very high burn value and is very good for burning as energy. If fuel use is not possible, the material takes very little airspace at a landfill.
Processing ragger wire is very profitable. One TANA customer is actually digging up their landfill for old ragger wire. They shred it and recover steel for extra income. The remaining plastic shred is used as fuel in their own facility.