By Laura Veneri | Published in Recover magazine no 5/2022
TANA 440DTeco shredder works at the Zito Plastica in Acerra shredding industrial plastic waste and car bumpers.
Acerra, province of Naples: “I knew the machine from seeing it at international trade fairs and as soon as I had the chance, I said to myself: why not try it out? It convinced me immediately”. We are guests of Vincenzo Zito at Zito Recupero Plastica Srl.
The company has been active since 1988 in the recovery of plastics, in particular PP, PE, PS, PET, PA, PC, HDPE, LDPE, car bumpers and tanks, scrap, blocks and sprues of all types of plastic and LDPE bales. Tough, difficult-to-process but high-quality plastics that can be recycled and given a new lease of life.
Born out of the environmental sensitivity of Vincenzo and his father, when numerous authorisations were not needed but just a lot of initiative, today Zito Plastica is a small industry in which several plastic recycling plants operate on an area of 10,000 m².
“We offer highly qualified raw materials to Italian companies that produce plastic granules, the polymeric compounds. Our business is part of the circular economy chain because in our plant we recover quality plastic, process it and sell it back to companies that reuse it as a raw material, closing the loop,” explains Zito. To do all this, Zito Plastica has recently purchased a TANA 440DTeco shredder for plastic waste from Tana Italia srl with the valuable collaboration of Officine Donatoni.
Plastics
The plastic taken back by Zito Plastica comes from private car dismantlers who mainly deliver car tanks and bumpers, Fiat supply companies that produce plastic waste from industrial processing, and Asia Napoli, which delivers damaged recycling bins. The company is equipped with 40 demountable containers, which it stores with third parties for the storage of waste. A quick replacement of the full container with an empty one is provided; this type of operation solves the problems of temporary storage on company premises and ensures that the hygiene and health conditions required by law are met. Zito Plastica also relies on associated haulage companies that collect plastic waste throughout Italy.
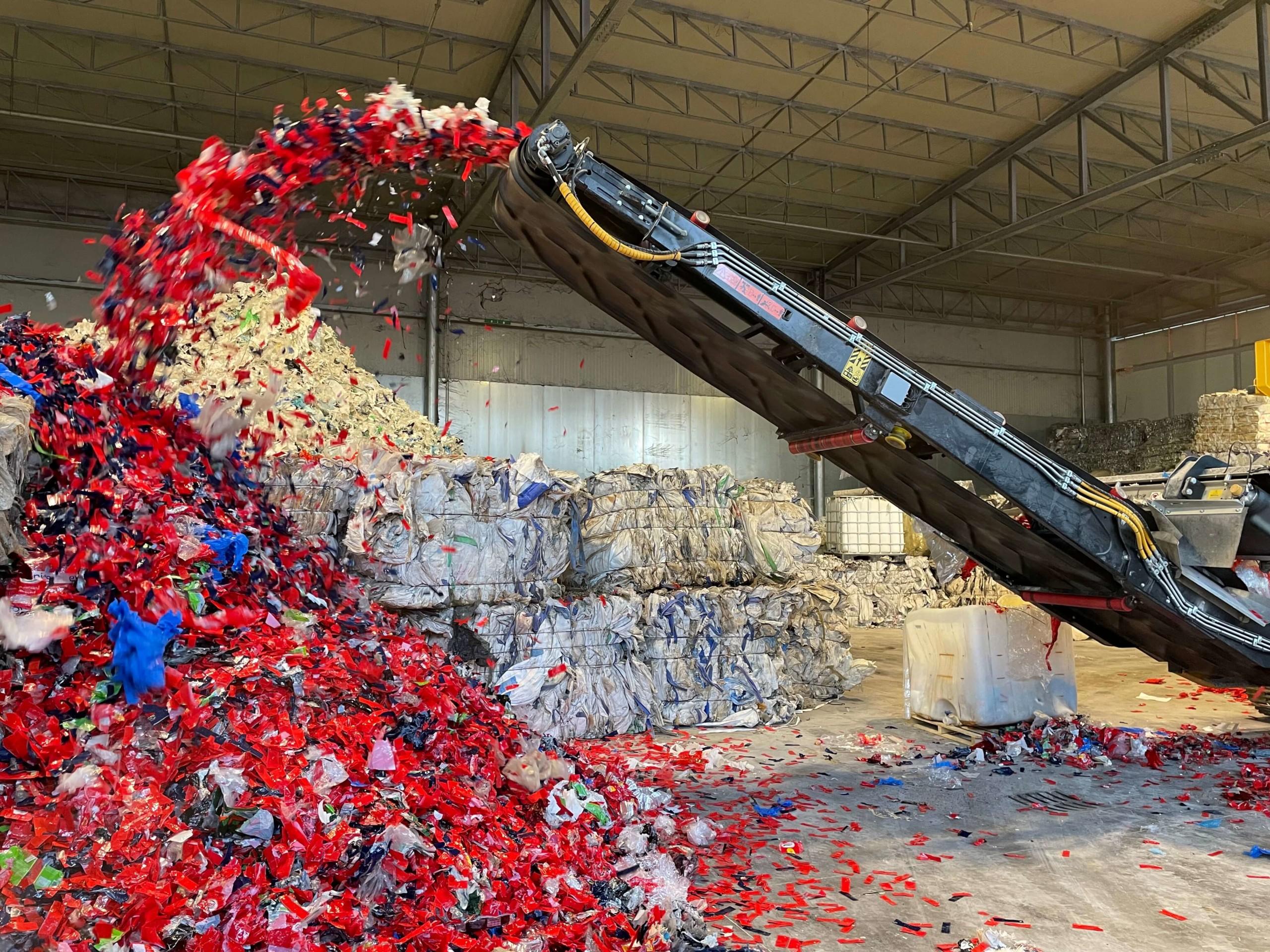
Processing stages
In the plant owned by Zito Plastica, which is authorised to process up to 21,000 tonnes of waste per year, the processing steps can be simplified into four stages. In the first stage, waste is sorted and divided according to the product category to which it belongs. The second stage involves shredding, volumetric reduction and separation of ferrous metals. This is where the TANA 440DTeco shredder comes into action. With a rotor 3 metres long and 90 centimetres in diameter, the largest in its category, the machine is able to handle any type of material, reducing the dimension to the defined size of the easily interchangeable grids. In this case a grid with 110 mm holes is used.
This initial processing makes the next step easier and faster. Once the material has been cleaned of ferrous metals and its particle size has been evened out, it is sent to a secondary shredder. Here it is further reduced in size without interruption and then processed in a refining and washing plant to obtain a product that meets the highest standards required by the plastic moulding and extrusion market.
The turning point with TANA
The need to increase production was the first reason for a shredder for plastic waste.
“We purchased the TANA shredder to cope with an increasing demand for material. The fixed plant used to process 3 tonnes per hour, but with this new machine we can achieve 10-15 tonnes preventing metal objects from entering the refineries and causing significant damage and slowdowns – Zito explains – The biggest difficulty in treating the waste collected and processed by us is the size. Think of waste bins or car mudguards or agricultural irrigation pipes. They are all of considerable size. We needed a machine with a very large feeding hopper that would supply the secondary shredder with pieces of a more homogeneous size.”
The second reason for opting for a mobile shredder is the possibility of moving the machine to customers and industries that, for reasons of privacy, do not allow the materials that need shredding to leave their premises. In such cases, Zito Plastica’s operators are ready to move the shredder to the site and work at the plant that requests it.
“As I said, I had never seen the TANA shredder at work,” says Zito. “I had tried other machines, but none gave me the results that TANA did on plastic. I was very satisfied from the very first stages of testing. The machine never freezes. We have tried other shredders that could not shred the material and got stuck. This has never happened with the TANA 440DTeco, and we have tested it with every type of material we pick up. The homogeneity of the output material is constant and perfectly adapted to our needs. Ultimately, it is very simple to use. I am very happy with the purchase and the support that Tana Italia and Officine Donatoni have given us”.
The TANA 440DTeco shredder was delivered to Zito Plastica in September 2021 and the operators who use it in the company are very happy with it because it is a very intuitive machine, and they can count on constant support.
“Production has increased so much that I will have to buy a refiner to meet the 440DT production,” concludes Zito.
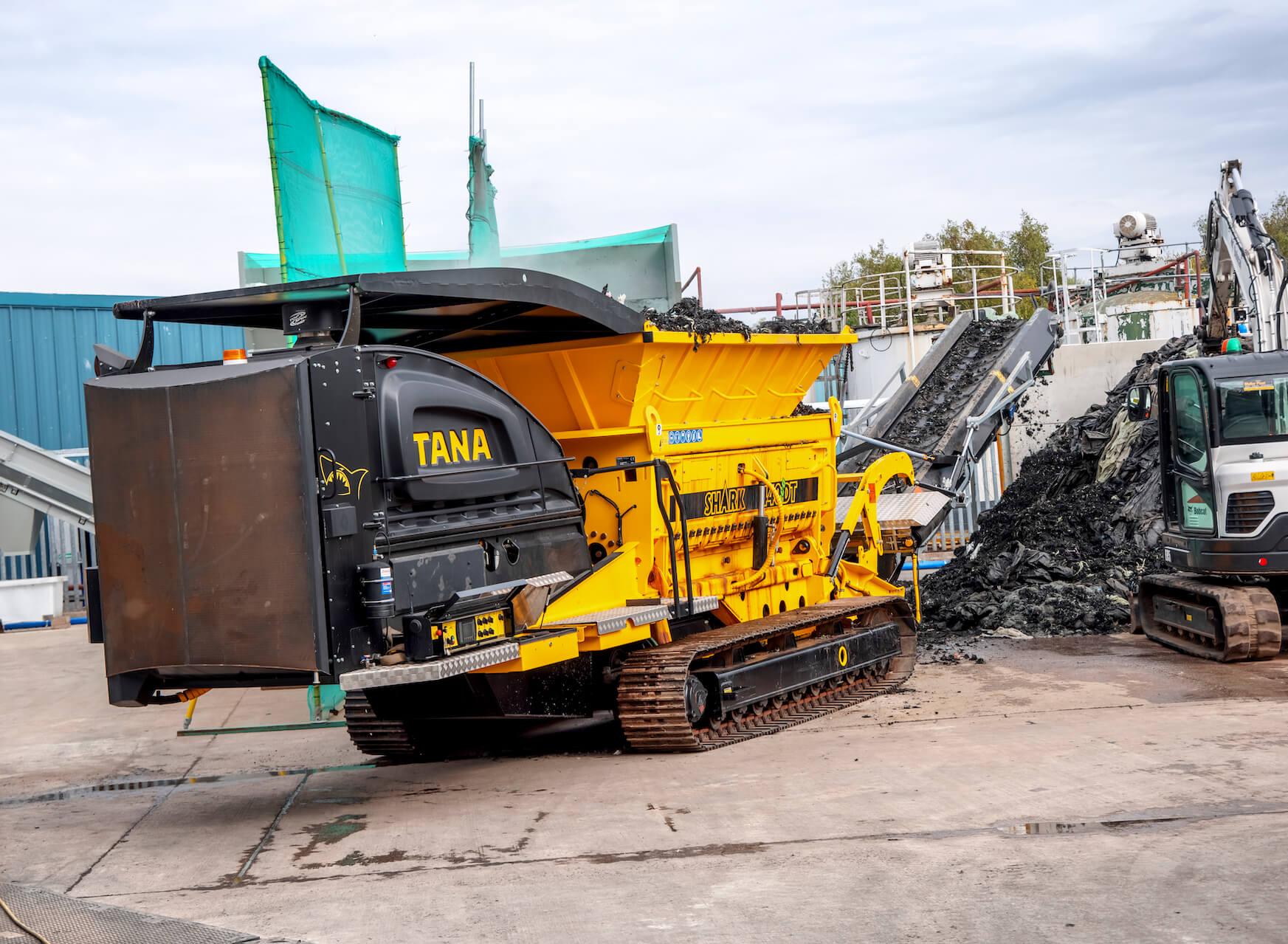
Le Officine Donatoni
Officine Donatoni, founded in 1978 by Ciro Donatoni, was born as a workshop for repairing self-propelled wheel loaders. In addition to routine maintenance work, the workshop also dealt over the years with total vehicle revision and mobile assistance in southern Italy. In 2009 with the integration of Alessandro Donatoni, in addition to the workshop sector, the company started to also sell equipment. Alessandro Donatoni takes care of buying and selling machinery useful in the field of recycling and ecology, both new and used.
The company’s strength is in following its customers, understanding their needs, directing them towards the equipment best suited to them, meeting their expectations and improving their production. Over the years, several agreements have been made with leading brands in the sector, so as to ensure a wide range of solutions for customers. One successful partnership is with Tana. The TANA shredder for plastic waste is useful for volumetric reduction of waste, ensure an increase in its value on the market. Higher quantities and a better-quality product, leading to higher earnings.
TANA 440 Series
The TANA 440 Series shredders are suitable for practically any type of solid waste material and especially excel at processing difficult waste, such as mattresses, tyres, plastic, cables and textiles. The design of the frame allows a lot of space between the conveyor and the rotor. The structure allows for a greater flow of material at the outlet, especially in the processing of bulky waste, such as plastic and mattresses. New feeding hopper design features a raised wall to prevent unshredded materials from falling onto the discharge conveyor.
The cleaning combs of the rotor are individually bolted on, and significantly reduce maintenance time and costs simplifying the operation of the machine. The shredder is controlled by the TCS (TANA Control System) touch screen display with e.g., the possibility of individually adjusting the conveyor speeds and the angle of the discharge conveyor even during operation.
The new TANA Control System (TCS) is equipped with a touch screen display mounted in a sheltered position and controls and manages all machine functions safely and immediately. The new user interface is extremely intuitive and enables the operator to easily set up the most efficient mode for each process. The new version of the TANA Control System (TCS) makes it possible to use the shredder and ensure precise and continuous control at every stage. The operating system can be updated remotely. TanaConnect®, also fitted as standard, allows you to remotely monitor every operational function of the machine, optimising the uptime and reducing operating costs as well as generating detailed reports of the most sensitive production data.