Pa-Ri Materia Oy is a company located in Finland, who use a TANA Shark slow-speed shredder for producing RDF (refuse-derived fuel) and occasionally waste wood. Their output is approximately 10 to 20 tons per hour, depending on the size of the rotor screen being used.
Pa-Ri Materia Oy started a completely new line of business with their TANA Shark shredders and they have successfully acquired efficiency and market shares by taking advantage of the mobility of the TANA shredder. The company has purchased another TANA Shark shredder and they use the other for pre-shredding and the other one of fine shredding. The versatility and the broad variety of screen sizes are in active use.
Pa-Ri Materia Oy is a contractor primarily utilizing the machine for production of RDF (refuse derived fuel) and occasionally for waste wood. For contracting they employ five people full time and three part time. RDF production is a challenging both in terms of the particle size and output. Particle size is often defined very precisely, and it needs to be homogeneous. Additionally, the output has got to be high enough. Neither one can be compromised.
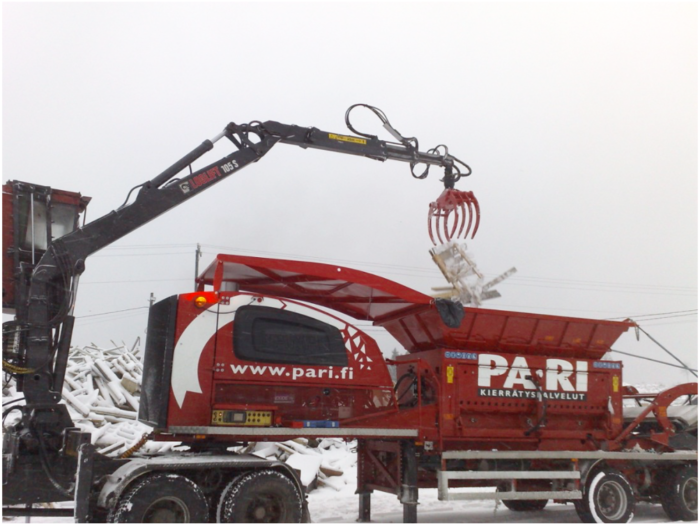
Pa-Ri Materia’s solution: using two TANA Sharks in line
When Pa-Ri Materia purchased TANA slow-speed shredder they were just about to start their business in materials handling. In their enthusiasm they also wanted to learn to use the machine in a most appropriate way.
“First we tried to teach the machine into our ways but finally we gave the machine a chance to teach us”, Ari Ala-Opas, the company’s Operations Manager states smiling and continues: “For instance, the right distance between the screen and rotor was systematically analyzed by adjusting it inch by inch and measuring the output produced in certain time.”
Often Pa-Ri uses the two TANA Sharks on-line. The pre-shredded material is fed directly from the first TANA shredder to the hopper of the other, equipped with either a 160 mm or a 200 mm rotor screen. In RDF production the rotor-to-screen clearance has got a major impact on the end product size but it affects the output, too. “The smaller the clearance is, the bigger the particle size, illogical but true “, tells Ala-Opas. Pa-Ri Materia uses habitually either a 160 mm screen or a 200 mm screen for RDF, 160 mm screen is so close to the rotor as possible, a 200 mm screen must be at least 150 mm away of the rotor, if it is closer, long particles start getting through.
Another thing affecting the output is how the two machines are placed on-line. This is also something that Ala-Opas found out by systematic trial. The angle of the conveyor and the hopper has got to be over 45 degrees. This ensures even spreading of the material on the rotor. And the machine has got to be placed to the back of the machine at the magnets side. If it is on the other side, bridging will occur.
What kind of output and particle size are we then talking about in RDF production? The quality of the material has a major impact on it. If there is some wood among the material, the average capacity in ongoing work is around 10 tons per hour, the particle size being 100×100 mm. This is received either with a 200 mm screen with a clearance of 150 mm or with a 160 mm screen and minimal clearance to the rotor. The only difference is that with the 160 mm screen the particle size is more homogeneous.
If there is no wood at all in the material it is advisable to use the 160 mm screen. With no wood the ongoing average capacity is 9-10 t/h, and particle size 80×80 mm. Wood helps to keep the screen clean but does not affect capacity as such. But when there is no wood, the screen has got to be taken out and cleaned every 2,5 hours, which diminishes capacity a bit. The adjustable screen is most useful when there is no wood in the material.
The output improves when there is more tolerance in the particle size. Without screen the real ongoing average capacity 20 tons per hour can easily be achieved and with 200 mm screen 14 tons per hour.
With the materials Pa-Ri material mostly shreds the adjustable screen has proven out to be of uttermost use in RDF production whereas with wood it is not so applicable. Ala-Opas also highlights the importance of daily maintenance and ware-part care in ensuring maximum benefits of TANA Shark – or any machine.