Value of recovery
TANA’s commitment to the environment
Article originally published in Recover IT magazine in Italian – TANA Stazionario Biomassa
Since the 1970s, at the dawn of organised waste management, northern Europe has been the driving force behind an environmental awareness whose importance has gradually been recognized globally, until it became a priority issue in every aspect of human activities. TANA was born out of the intuition of a young entrepreneur, Matti Sinkkonen, who developed the first landfill compactor in 1971, the ancestor of a series of machines that still today, in ever more evolved versions, represent the state of the art in that machine segment.
The need for shredding was born from empirical waste management leading to technological evolution and awareness of the vast resources available from proper waste management. In 2006, TANA produced the first single-rotor primary shredder. Even before creating ‘a machine’, the aim was and still is to implement an extremely powerful, fully hydrostatic tool with a truly unique versatility, capable of working on the most diverse materials to achieve the set objectives.
From that original design comes the current evolution of the TANA440 shredder, with electric motor or diesel engine, in mobile tracked, semi-trailer, or stationary versions. Keep on reading to find out why it is called a TANA 440 and how the stationary version of a TANA shredder can be used in biomass processing.
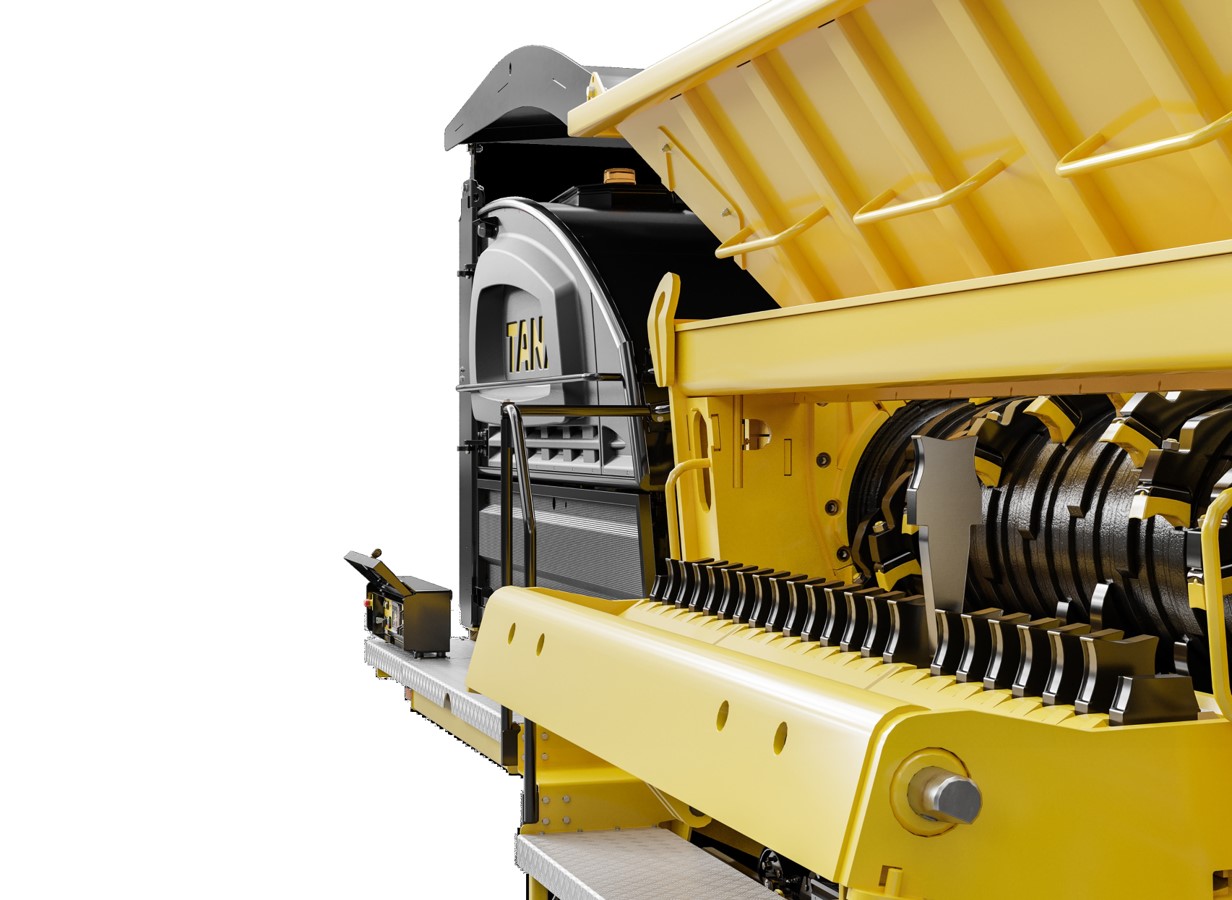
TANA 440 Series
Why 440? It could simply be an acronym, a nickname. It actually represents the maximum shredding force per tooth expressed in kN. It remains a theoretical figure, it is true, but it is the highest breaking load of all shredders in this category on the market.
This means that the 3 metre by 900 mm diameter of the rotor, the largest in its class, offers maximum aggressiveness on the material, limiting inversions to maintaining maximum shredding efficiency and in extreme cases protecting the machine from accidental breakage.
Despite the most careful checks, the presence of unbreakable foreign bodies cannot be ruled out: metal objects, lost tools, stones, etc., which can cause extensive damage and long downtimes if the treatment facilities do not have the necessary protection.
And here emerges one of the most interesting aspects of the TANA440 shredder. The complex sensitivity of the electro-hydraulic traction system allows maximum power to be expressed at all times on materials to be shredded, but maintains the capacity to stop and reverse rotation when the machine is subjected to potentially damaging breaking loads. A sturdy, hydraulically opening hold door allows immediate inspection of the shredding area from the ground, extracting any foreign bodies and quickly getting the machine back to work.
Size control is also a feature that makes the TANA440 extremely versatile.
The ability to install and replace size control screen quickly and efficiently is another aspect that makes the TANA440 unique.
From 50 mm up to 275 mm, you can define the size best suited to your needs by replacing the perforated control screens quickly and safely. By completely excluding the screens, the shredder can freely express all its power, achieving top levels of production on all types of material.
The material shredded in this way also makes the subsequent iron removal more efficient, as it has a smoothly flowing, well-defined grain size even in large sizes.
The TANA440 series is irreplaceable especially when processing ‘difficult’ materials: mattresses, tyres, plastics, extrusion risers, cables and textiles. The special design of the frame allows a wide space between the rotor and the discharge conveyor, enabling a smooth passage of the outgoing material even when this could become a problem, as in the case of mattresses and bulky items in general.
The standard hopper with its new design features a raised, hydraulically tilting wall that prevents unshredded material from falling onto the incline conveyor.
Particular attention has been paid to the scrapers cleaning the rotor that efficiently remove all those materials that tend to coil up escaping shredding and risk slowing down or sometimes blocking operations. Individually bolted, they significantly reduce maintenance time and costs by simplifying operations.
The entire dedicated TANA TCS system is operated via a large, intuitive touch screen that provides a quick overview of the machine’s functions at all times and ensures that every single operational function of the machine can be quickly set up even during work phases.
Today’s requirements call for constant and direct monitoring of each machine by management, which is why TANA has implemented its own TanaConnect® operating system, through which all operational functions, alarms and machine-related maintenance can be checked and managed remotely, generating detailed reports. Unique in the world, TANA has embraced the demands and dictates of the ‘Industry 4.0’ protocol and is able to offer its own upgrade to meet the requirements without installing third-party tools.
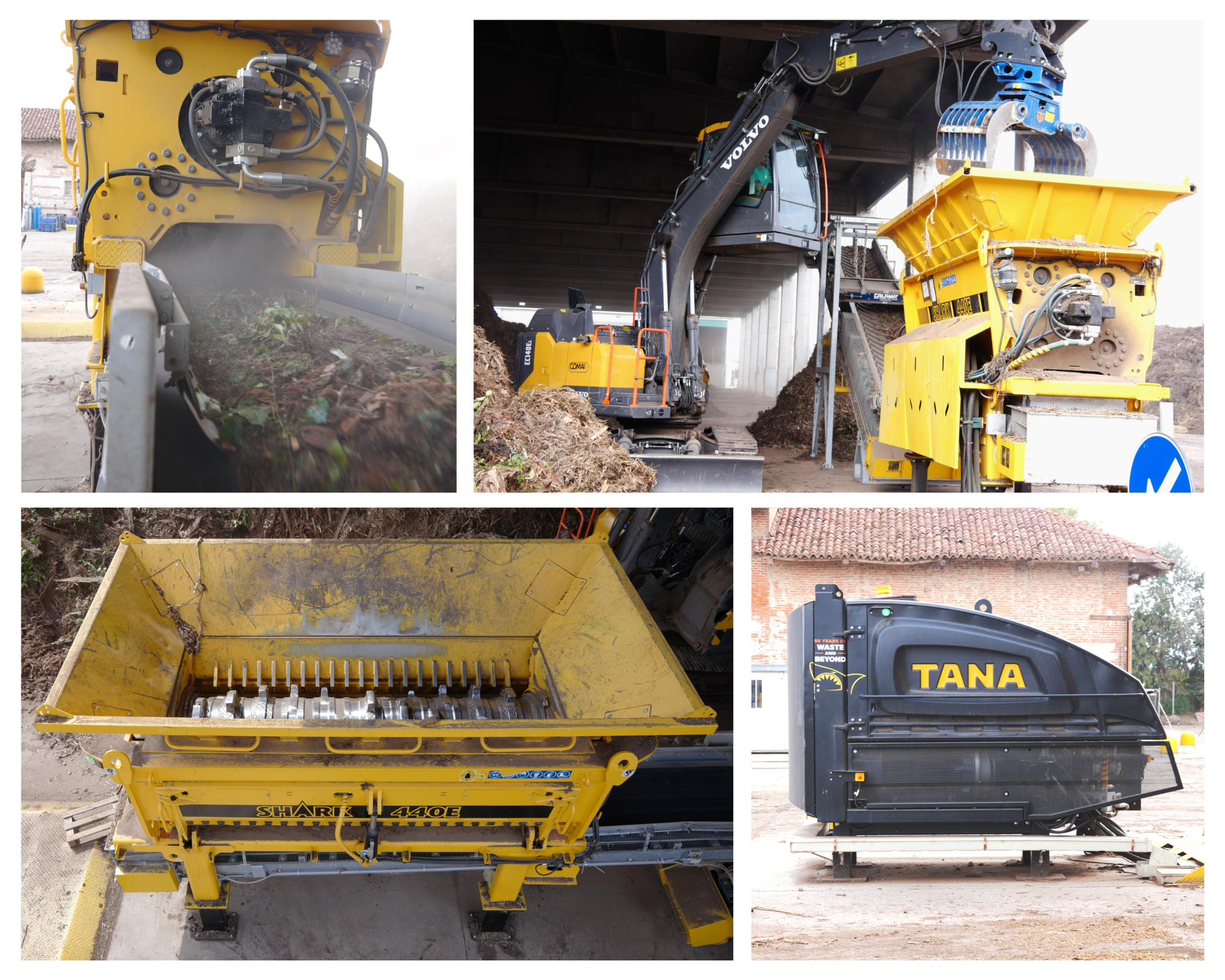
The stationary version for biomass processing
Biomass processing is one application where the TANA 440 has once again decisively demonstrated its potential and efficiency.
Together with COMAI spa, TANA Italia‘s dealer for the North-West, we have analysed in depth some of the customer’s particular requirements and, based on the results of the field tests, we set up an efficient stationary system at the Azienda Agricola Galatero in Cervignasco (CN), where the TANA440E shredder expresses all its potential in terms of productivity, shredding quality, and ease of management and maintenance.
Platforms authorised for the treatment of biomass receive various materials that comply with the requirements, and in this specific case the system is intended for the treatment of materials ranging from so-called green, grass and branches, to tree trunks and stumps resulting from uprooting, to be composted and reused as soil improver for agricultural crops.
Maximum attention has been paid to the unavoidable presence of foreign bodies that could affect the integrity of the machine if not adequately protected.
The special sensitivity of the TANA440E‘s electro-hydraulic drive system maintains maximum aggressiveness on materials at all times and a high level of protection against accidental breakage caused by unbreakable bodies. In such cases, the possibility of being able to intervene immediately, inspect the shredding area from the ground via the hold door, extract any foreign bodies and quickly get the machine back to work is truly amazing.
The stationary application also offers undoubtable advantages, especially in systems with high homogenous material flows, and the features of the TANA440E shredding unit are further enhanced by the possibility of installing wide extraction and discharge conveyors as well as iron removal belts.
The electrical system of the belts and the hydraulics of the shredder are fully integrated in terms of management and safety with a dedicated control unit. In any case, this type of system also benefits fully from all ‘Industry 4.0’ specifications that TANA offers and can be easily integrated into more complex systems in any field of application.
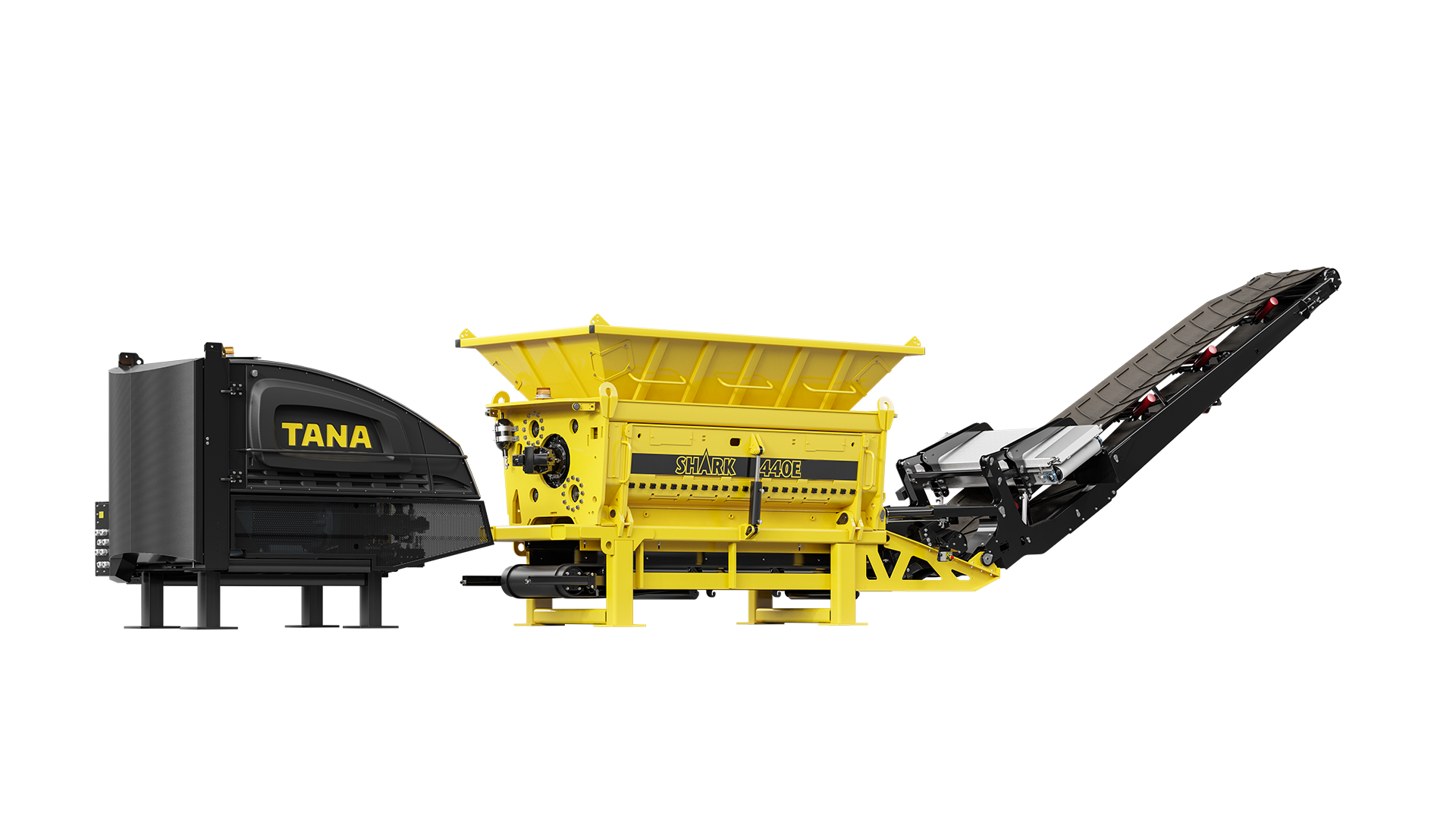